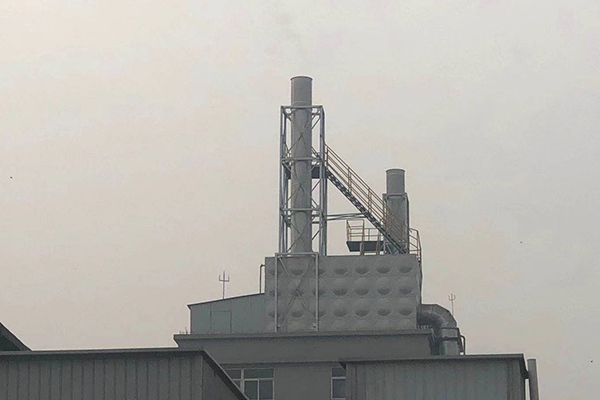
RCO organic waste gas catalytic combustion purification equipment can effectively purify the environment, pollution, improve labor operating conditions, ensure the health of workers, and the heat emitted can be recycled to reduce production costs. RCO organic waste gas catalytic combustion equipment has perfect system design, complete auxiliary equipment, high purification efficiency and high automation. RCO organic waste gas catalytic combustion equipment RCO organic waste gas catalytic combustion purification device is designed based on two basic principles of adsorption and catalytic combustion, namely adsorption concentration catalytic combustion method. The dedusting equipment adopts the working mode of single bed adsorption purification of organic waste gas and catalytic combustion device regeneration and activation of activated carbon. Firstly, the organic waste gas with low concentration is adsorbed by activated carbon, and the adsorption operation is stopped when it is almost saturated, then the organic matter is desorbed from the activated carbon by hot gas flow to regenerate the activated carbon; The desorbed organic matter has been concentrated (the concentration is dozens of times higher than the original) and sent to the catalytic combustion chamber for catalytic conversion into CO2 and H2O for emission; When the concentration of organic waste gas reaches above 2000ppm, the organic waste gas can maintain spontaneous combustion in the catalytic bed without external heating. Some of the burned tail gas is discharged into the atmosphere, and most of it is sent to the adsorption bed for desorption and regeneration of activated carbon. In this way, the heat energy required for combustion and desorption can be met to save energy. The regenerated activated carbon can be used for the next adsorption.? RCO organic waste gas catalytic combustion equipment uses catalytic combustion method to convert toxic and harmful organic gas into non-toxic gas.? The main structure of RCO organic waste gas catalytic combustion equipment is composed of three major parts: purification device host, induced draft fan and control system. The catalytic combustion purification device includes: dedusting flame arrester, heat exchanger, preheater and catalytic combustion chamber. The organic waste gas enters the preprocessor from the air inlet at the upper part of the equipment, passes through the coarse filter element composed of multi-layer stainless steel wire mesh to remove dust and other particles in the waste gas, and enters the combined adsorption bed from the main channel at the lower part of the device (two rows in parallel with six grids). Each adsorption bed is equipped with a set of pneumatic switch valve, which can change the adsorption bed into adsorption/desorption state. The longitudinal section of the adsorption bed from bottom to top is respectively the inlet manifold, adsorption chamber, air purification chamber and outlet manifold. The adsorption chamber and the air purification chamber are separated by a flower plate, under which a number of adsorption cylinders are hoisted. The waste gas entering the adsorption chamber passes through the adsorption layer through the outer wall of the adsorption cylinder, VOCs molecules are adsorbed by a large number of microporous surfaces of the adsorbent. After being purified, the waste gas enters the purification chamber upward through the flower plate hole, and then enters the gas outlet header through the switching valve and is discharged by the fan. One of the six adsorption chambers must be in the desorption state, and the other five must be in the adsorption state. Generally, the desorption time is 12 minutes, that is, the adsorption bed responsible for the adsorption work can be desorbed and regenerated once every hour. This work process of the device coincides with the name of the invention zhuanli - a kind of compartment offline desorption bag type adsorption equipment. Its process principle is the same as that of the pulse reverse blow compartment offline bag type dust collector, except that the purification process of the device is "physical adsorption", The bag filter purification process is "physical filtration". The desorption working medium of the adsorption bed is hot air, which is provided by the catalytic combustion device. Generally, the temperature of the hot air is ≤ 150 ℃, which is determined by the boiling point of different VOCs and the saturated vapor partial pressure at the desorption temperature.
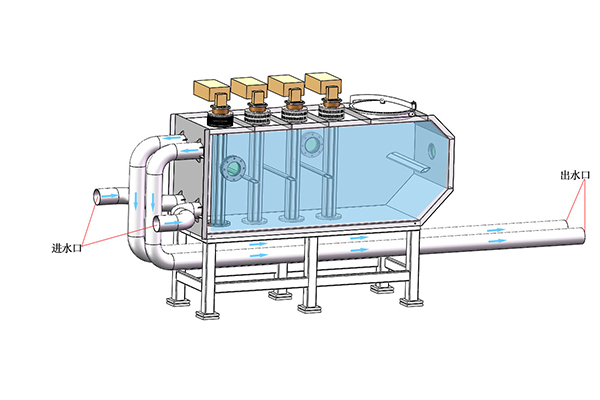
Microwave and ultraviolet water treatment equipment can improve heat exchange efficiency, save energy and reduce consumption. production Microwave drying equipment The deposits on the surface of the cooler rise by 0. mm every time, High efficiency of heat exchanger can generally reduce 20-30%, and power consumption will increase 4-8%. The selection of organic chemical dosing method can maintain the equipment and extend the service life of the equipment. The etching rate of carbon steel by cooling circulating water without microwave ultraviolet water treatment equipment exceeds 0.5mm/a, Microwave drying equipment programme The corrosion rate of the solved cooling circulating water on carbon steel is less than 0. mm/a, which can reasonably maintain the equipment and extend the service life of the equipment. Reduce the frequency of routine maintenance to ensure normal operation.
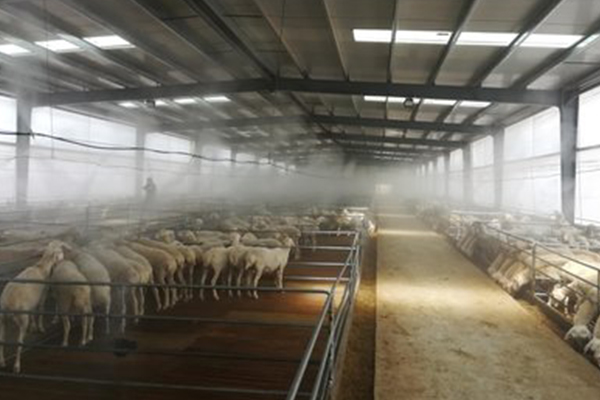
Because of the high intensity of water bodies in North China, the cooling and circulating water for central air conditioning is cooled by drinking water, production Microwave drying equipment The common phenomenon is scaling, oxygen erosion and microbial sludge. The purpose of the microwave ultraviolet water treatment equipment is to reduce the three major drawbacks of scaling, erosion and algae growth, which requires the addition of various drugs to the system software, Microwave drying equipment programme According to the working conditions of equipment, materials and water bodies in various regions of various enterprises, the Drug Secret 1 prescription should be effectively matched to improve quality and efficiency, stabilize water bodies and achieve synergy, reduce the amount of drug sludge and sewage microwave ultraviolet water treatment equipment, control costs, and achieve the goal of water conservation, energy conservation and prolonging the service life of equipment.
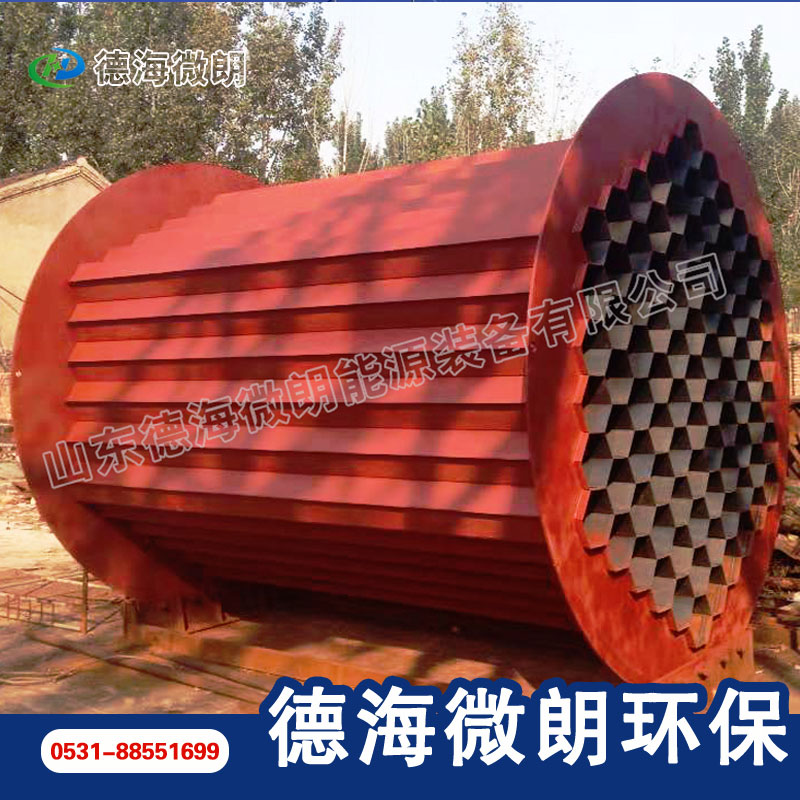
Ultraviolet disinfection belongs to physical instant disinfection technology, which can keep sterile under the condition that the water body is not polluted. When the treated water leaves the disinfection reactor, production Microwave drying equipment Some microorganisms killed by ultraviolet light will repair damaged molecules and regenerate bacteria under visible light irradiation, which is called light reactivation. Microwave drying equipment programme Some bacteria can also repair themselves under the condition of no light, that is, dark reactivation. According to the current research results, photoreactivation is the main way of most microbial remediation and also the main control target.
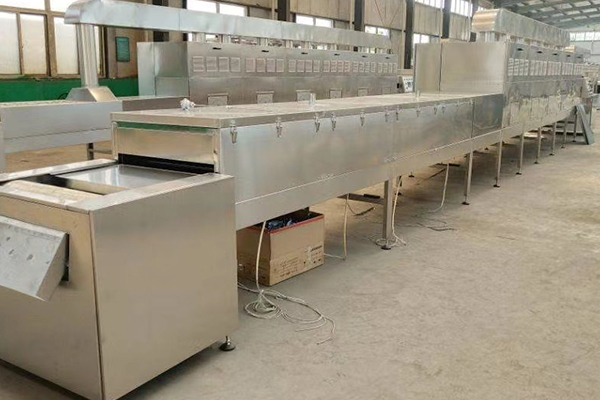
What are the common faults of microwave and ultraviolet water treatment equipment, production Microwave drying equipment Leakage in the water pressure drop equipment system, lack of pressure at the inlet of the high-pressure pump, air leakage, water leakage, blockage of the filter element of the precision filter, high-pressure pump fault, etc. may cause the water pressure drop of the equipment. Solution: Overhaul the high-pressure pump and precision filter, and eliminate problems. Microwave drying equipment programme The increase of equipment water pressure may be due to the error of high-pressure pump outlet scheduling index and the blockage of the pipeline from high-pressure pump to reverse osmosis equipment. Solution: recover the equipment pressure by dispatching the outlet index of the high-pressure pump and cleaning the pipeline between the high-pressure pump and the reverse osmosis equipment. The decrease in water production of the manufacturers of microwave and ultraviolet water treatment equipment may be due to the lower water temperature, lower water pressure, and pollution and blockage of the reverse osmosis membrane. Solution: recover normal production by adjusting the temperature of raw water and cleaning and replacing the reverse osmosis membrane.