Microwave and ultraviolet water treatment equipment can improve heat exchange efficiency, save energy and reduce consumption. Customized Ultraviolet sterilization equipment The deposits on the surface of the cooler rise by 0. mm every time, High efficiency of heat exchanger can generally reduce 20-30%, and power consumption will increase 4-8%. The selection of organic chemical dosing method can maintain the equipment and extend the service life of the equipment. The etching rate of carbon steel by cooling circulating water without microwave ultraviolet water treatment equipment exceeds 0.5mm/a, Ultraviolet sterilization equipment programme The corrosion rate of the solved cooling circulating water on carbon steel is less than 0. mm/a, which can reasonably maintain the equipment and extend the service life of the equipment. Reduce the frequency of routine maintenance to ensure normal operation.
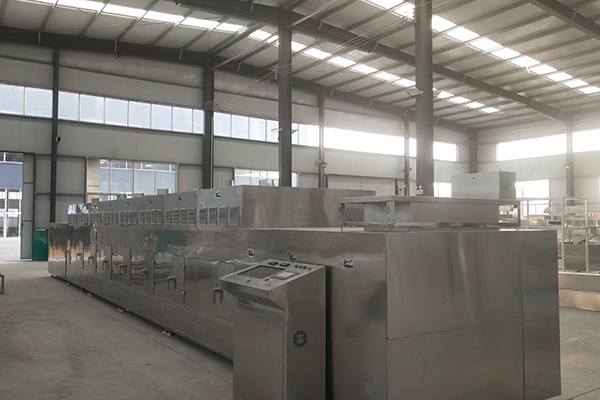
1. The welding of equipment shell and framework shall be firm without obvious deformation or burn through defects. 2. The equipment surface shall be evenly sprayed with the same color, and the surface shall be free of flow marks, bubbles, paint leakage and peeling. 3. The appearance of the equipment shall be neat and beautiful without obvious hammer marks and unevenness. The panel instruments, switches, indicator lights and labels shall be installed firmly and correctly. In order to ensure the stability of the equipment, we need to replace the lamp regularly, Customized Ultraviolet sterilization equipment The imported lamp should be replaced after 9000 hours of continuous service or one year to ensure a high disinfection rate. Ultraviolet sterilization equipment programme When replacing the lamp tube, first pull out the power socket of the lamp tube, pull out the lamp tube, then carefully insert the cleaned new lamp tube into the sterilizer, install the gasket, check for water leakage, and then plug in the power supply. Be careful not to touch the quartz glass of the new lamp tube with your fingers, otherwise the disinfection effect will be affected due to stains.
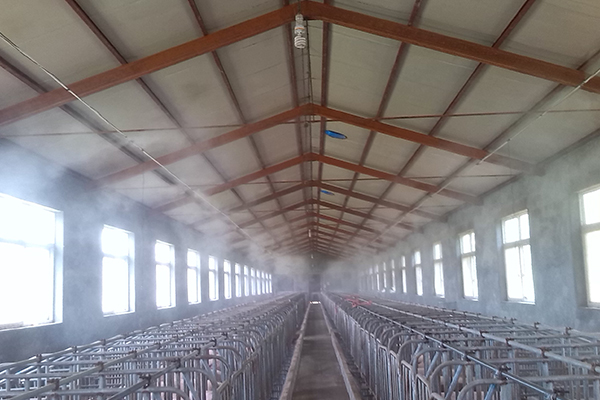
The catalytic combustion equipment for waste gas treatment is mainly used as a supporting part of the catalytic bed electric heating oxidation combustion system in the CO/RCO adsorption+desorption+catalytic combustion system. It is widely applicable to the purification and odor elimination of hazardous waste gas volatilized or leaked from painting, printing, household appliances, footwear, plastics and various chemical workshops, and is suitable for low concentration (1501000) The organic waste gas that is not suitable for direct combustion or catalytic combustion and recovery treatment will be concentrated by activated carbon adsorption, and then the high concentration organic waste gas will be removed through the desorption procedure and sent to the unit for thermal oxidation reaction. The self heating effect of the organic waste gas catalytic reaction can greatly reduce the heat consumption of the electric heater, especially for the treatment sites with large air volume, Satisfactory economic and social benefits can be obtained. Application scope of exhaust gas catalytic combustion equipment: 1. Industrial applications: common pollutants discharged from petrochemical, light industry, plastics, printing, coating and other industries; 2. Waste gas type application: hydrocarbon compounds (aromatics, alkanes, olefins), benzene, ketones, phenols, alcohols, ethers, alkanes and other compounds; Features of catalytic combustion equipment for waste gas treatment: 1. Convenient operation: fully automatic control during operation. 2. Low energy consumption: during normal operation, the equipment operates at low power (or no power) because the exhaust gas has some concentration. 3. Stable performance: pressure relief and self protection, fire resistance and dust removal, over temperature alarm and automatic control. 4. Low resistance: honeycomb ceramic catalyst impregnated with today's advanced precious metal palladium and platinum has a large specific surface area. 5. Small floor area: only 70% of the same products in the same industry. 6. Long service life: the catalyst is usually replaced within 4 years
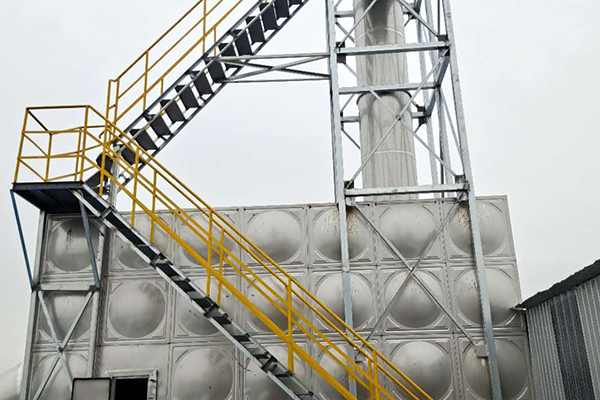
I. Efficient deodorization II. No substances need to be added III. Strong adaptability IV. Low operation cost V. No treatment VI. Small area of equipment VII. Manufacturing of high-quality imported materials