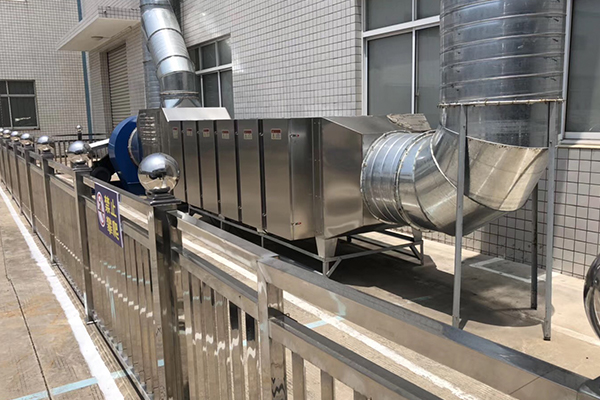
To solve the problem of light reactivation: open the channel to realize underground water outflow, to avoid or reduce the visibility of treated water before entering the pipeline. At the same time, use a dark container containing a sample of test water, new type Deodorization of industrial waste gas It shall be sent for inspection in time to avoid factors such as storage conditions or test time affecting the test results. Improve the light transmittance: adjust the front-end treatment process to reduce the SS mass concentration of water in the UV disinfection device, Deodorization of industrial waste gas manufactor The ultraviolet disinfection I was adjusted to ozone decolorization, which reduced the chromaticity of the influent water to ensure that SS was controlled below 10 mg/L; The front-end technology has been adjusted to strictly control the consumption of PAM and other chemicals, and a defoaming device has been installed at the water inlet of the external disinfection device to reduce the foam content in the water body and increase the light transmittance of the water body.
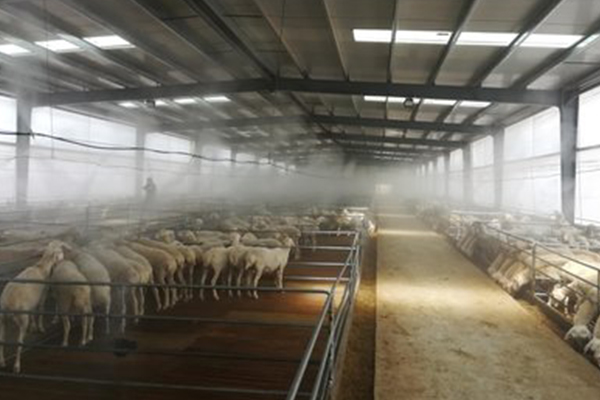
Activated carbon adsorption and catalytic combustion equipment is a common volatile organic waste gas treatment equipment. It is energy-saving, environmental protection, no secondary pollution, and high purification efficiency. It is a very good equipment for VOC waste gas treatment. Generally, the main composition of activated carbon adsorption catalytic combustion equipment is as follows: Pretreatment equipment: since honeycomb activated carbon adsorption requires specific conditions such as temperature, humidity and cleanliness, it is necessary to treat the organic waste gas with different characteristics before entering the activated carbon adsorption. The organic waste gas containing more dust particles needs to be filtered. The waste gas with a temperature greater than 45 ℃ needs to be cooled, and the waste gas containing a large number of water mist particles needs to be separated and filtered. Activated carbon adsorption bed: it can absorb organic waste gas by taking advantage of the porous physical characteristics of activated carbon. The design of the adsorption bed follows the law of two-phase adsorption curve. Only by combining the amount of activated carbon and calculating the cross section wind speed and retention time of activated carbon adsorption can the adsorption efficiency meet the design requirements and meet the emission standards. The box is in negative pressure state during equipment operation, and it is required to be air tight. The desorption temperature of the box is between 70-100 ℃ during the desorption process, and the heat preservation is generally 50mm considering the energy saving and safety factors. Ensure that the temperature of the outer wall of the box is not higher than the normal temperature by 15 ℃. Main exhaust fan: as the main power of the equipment, the exhaust fan guides the air to move according to the specified process. The fan can be selected accurately only when it is stable and reliable, and the resistance calculation of the system is accurate. The operation of the fan will produce noise, and the high-power fan needs to be equipped with a sound insulation room. Attention shall be paid to the design that the wind speed at the air outlet shall not be too high. Catalytic combustion equipment: after the system has operated for a period of time, the activated carbon needs to be regenerated after adsorption saturation to restore the adsorption activity of the activated carbon. The organic waste gas is concentrated in the activated carbon. After the organic matter is separated from the activated carbon layer at low temperature, it is decomposed into water and carbon dioxide at about 300 ℃ through the action of catalyst. At the same time, the energy is released. The energy is replaced by the heat exchange device to maintain the energy of spontaneous combustion of the equipment. For a single activated carbon adsorption bed, the desorption time is 2-2.5 hours. The set time of activated carbon adsorption box is automatically switched to desorption regularly. The service life of the ceramic honeycomb noble metal catalyst loaded inside is 8000 hours. The whole desorption system adopts multi-point temperature control to ensure the stability of desorption effect. The selection of organic waste gas catalyst is the core of this equipment. Valve switching system: valves include adsorption system valve, desorption system valve, cooling and emergency discharge valve. The three types of valves are required to be timely and accordingly to ensure that the air leakage rate is less than 2%. The conventional galvanized sheet air valve in the market has air leakage due to unreliable sealing, so it is necessary to select the high temperature resistant air valve with silicone gasket. The temperature is reliable when opening and closing the valve. Due to the temperature of the gas through which the valve passes, it is very easy for conventional plastic electric actuators to age and deform, resulting in ineffective execution. Generally, long rod actuators are used.
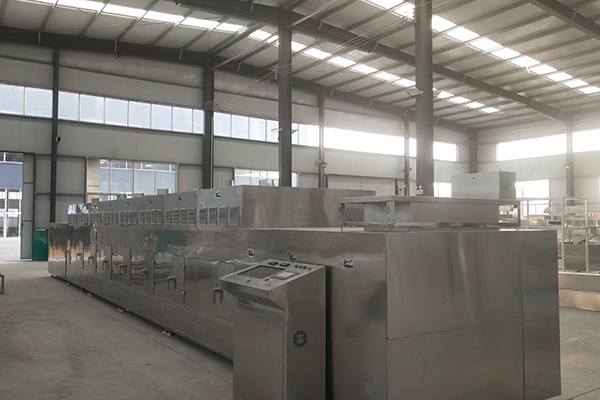
Have you ever thought about whether you need a sterilizer on your water tank? If so, which Z is better? An aquarium scientist's differences between ozone and ultraviolet sterilizers. Ozone is a gas composed of three oxygen atoms, while the oxygen we breathe is composed of two oxygen atoms. This chemical structure makes ozone highly active, new type Deodorization of industrial waste gas That's why it's such a powerful sterilizer. Deodorization of industrial waste gas manufactor It is meaningful that the bulb in the UV germicidal lamp is made of quartz, because quartz will not filter out the UV rays. However, water filters light according to its depth. Therefore, the water flow space between the quartz bulb and the external glass or plastic tube is usually only a few millimeters - a thicker space will reduce the intensity of ultraviolet rays and allow bacteria and other microorganisms to survive.
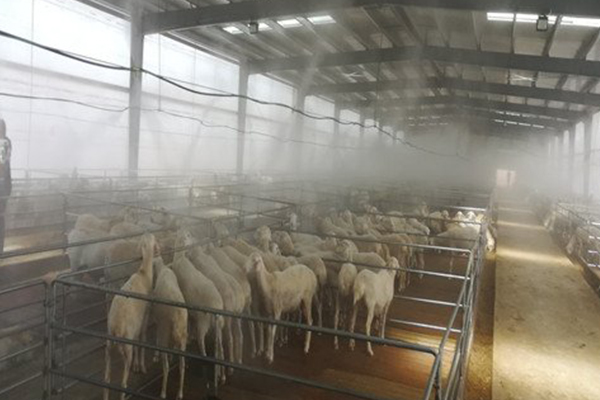
I. Efficient deodorization II. No substances need to be added III. Strong adaptability IV. Low operation cost V. No treatment VI. Small area of equipment VII. Manufacturing of high-quality imported materials