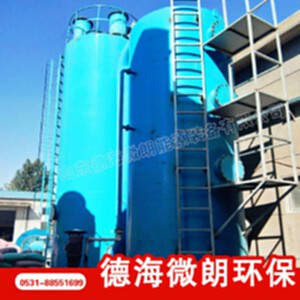
RCO organic waste gas catalytic combustion purification equipment can effectively purify the environment, pollution, improve labor operating conditions, ensure the health of workers, and the heat emitted can be recycled to reduce production costs. RCO organic waste gas catalytic combustion equipment has perfect system design, complete auxiliary equipment, high purification efficiency and high automation. RCO organic waste gas catalytic combustion equipment RCO organic waste gas catalytic combustion purification device is designed based on two basic principles of adsorption and catalytic combustion, namely adsorption concentration catalytic combustion method. The dedusting equipment adopts the working mode of single bed adsorption purification of organic waste gas and catalytic combustion device regeneration and activation of activated carbon. Firstly, the organic waste gas with low concentration is adsorbed by activated carbon, and the adsorption operation is stopped when it is almost saturated, then the organic matter is desorbed from the activated carbon by hot gas flow to regenerate the activated carbon; The desorbed organic matter has been concentrated (the concentration is dozens of times higher than the original) and sent to the catalytic combustion chamber for catalytic conversion into CO2 and H2O for emission; When the concentration of organic waste gas reaches above 2000ppm, the organic waste gas can maintain spontaneous combustion in the catalytic bed without external heating. Some of the burned tail gas is discharged into the atmosphere, and most of it is sent to the adsorption bed for desorption and regeneration of activated carbon. In this way, the heat energy required for combustion and desorption can be met to save energy. The regenerated activated carbon can be used for the next adsorption.? RCO organic waste gas catalytic combustion equipment uses catalytic combustion method to convert toxic and harmful organic gas into non-toxic gas.? The main structure of RCO organic waste gas catalytic combustion equipment is composed of three major parts: purification device host, induced draft fan and control system. The catalytic combustion purification device includes: dedusting flame arrester, heat exchanger, preheater and catalytic combustion chamber. The organic waste gas enters the preprocessor from the air inlet at the upper part of the equipment, passes through the coarse filter element composed of multi-layer stainless steel wire mesh to remove dust and other particles in the waste gas, and enters the combined adsorption bed from the main channel at the lower part of the device (two rows in parallel with six grids). Each adsorption bed is equipped with a set of pneumatic switch valve, which can change the adsorption bed into adsorption/desorption state. The longitudinal section of the adsorption bed from bottom to top is respectively the inlet manifold, adsorption chamber, air purification chamber and outlet manifold. The adsorption chamber and the air purification chamber are separated by a flower plate, under which a number of adsorption cylinders are hoisted. The waste gas entering the adsorption chamber passes through the adsorption layer through the outer wall of the adsorption cylinder, VOCs are adsorbed by a large number of microporous surfaces of the adsorbent, and the waste gas is purified and then enters the air purification chamber upward through the flower plate holes, Then it enters the main outlet pipe through the switching valve and is discharged by the fan. One of the six adsorption chambers must be in the desorption state, and the other five must be in the adsorption state. Generally, the desorption time is 12 minutes, that is, the adsorption bed responsible for the adsorption work can be desorbed and regenerated once every hour. This work process of the device coincides with the name of the invention zhuanli - a kind of compartment offline desorption bag type adsorption equipment. Its process principle is the same as that of the pulse reverse blow compartment offline bag type dust collector, except that the purification process of the device is "physical adsorption", The bag filter purification process is "physical filtration". The desorption working medium of the adsorption bed is hot air, which is provided by the catalytic combustion device. Generally, the temperature of the hot air is ≤ 150 ℃, which is determined by the boiling point of different VOCs and the saturated vapor partial pressure at the desorption temperature.
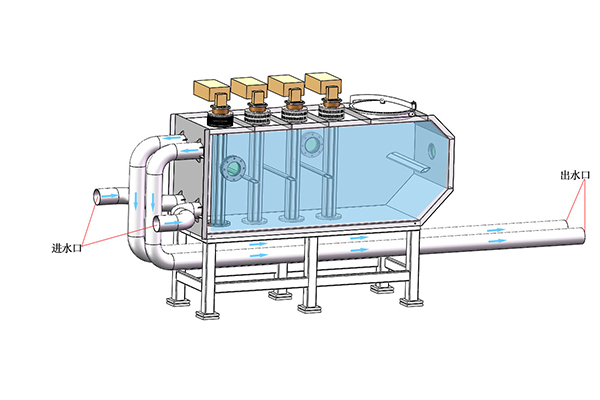
Activated carbon adsorption and catalytic combustion equipment is a common volatile organic waste gas treatment equipment. It is energy-saving, environmental protection, no secondary pollution, and high purification efficiency. It is a very good equipment for VOC waste gas treatment. Generally, the main components of activated carbon adsorption catalytic combustion equipment are as follows: Pretreatment equipment: since honeycomb activated carbon adsorption requires specific conditions such as temperature, humidity and cleanliness, it is necessary to treat the organic waste gas with different characteristics before entering the activated carbon adsorption. The organic waste gas containing more dust particles needs to be filtered. The waste gas with a temperature greater than 45 ℃ needs to be cooled, and the waste gas containing a large number of water mist particles needs to be separated and filtered. Activated carbon adsorption bed: it can absorb organic waste gas by taking advantage of the porous physical characteristics of activated carbon. The design of the adsorption bed follows the law of two-phase adsorption curve. Only by combining the amount of activated carbon and calculating the cross section wind speed and retention time of activated carbon adsorption can the adsorption efficiency meet the design requirements and meet the emission standards. The box is in negative pressure state during equipment operation, and it is required to be air tight. The desorption temperature of the box is between 70-100 ℃ during the desorption process, and the heat preservation is generally 50mm considering the energy saving and safety factors. Ensure that the temperature of the outer wall of the box is not higher than the normal temperature by 15 ℃. Main exhaust fan: as the main power of the equipment, the exhaust fan guides the air to move according to the specified process. The fan can be selected accurately only when it is stable and reliable, and the resistance calculation of the system is accurate. The operation of the fan will produce noise, and the high-power fan needs to be equipped with a sound insulation room. Attention shall be paid to the design that the wind speed at the air outlet shall not be too high. Catalytic combustion equipment: after the system has operated for a period of time, the activated carbon needs to be regenerated after adsorption saturation to restore the adsorption activity of the activated carbon. The organic waste gas is concentrated in the activated carbon. After the organic matter is separated from the activated carbon layer at low temperature, it is decomposed into water and carbon dioxide at about 300 ℃ through the action of catalyst. At the same time, the energy is released. The energy is replaced by the heat exchange device to maintain the energy of spontaneous combustion of the equipment. For a single activated carbon adsorption bed, the desorption time is 2-2.5 hours. The set time of activated carbon adsorption box is automatically switched to desorption regularly. The service life of the ceramic honeycomb noble metal catalyst loaded inside is 8000 hours. The whole desorption system adopts multi-point temperature control to ensure the stability of desorption effect. The selection of organic waste gas catalyst is the core of this equipment. Valve switching system: valves include adsorption system valve, desorption system valve, cooling and emergency discharge valve. The three types of valves are required to be timely and accordingly to ensure that the air leakage rate is less than 2%. The conventional galvanized sheet air valve in the market has air leakage due to unreliable sealing, so it is necessary to select the high temperature resistant air valve with silicone gasket. The temperature is reliable when opening and closing the valve. Due to the temperature of the gas through which the valve passes, it is very easy for conventional plastic electric actuators to age and deform, resulting in ineffective execution. Generally, long rod actuators are used.
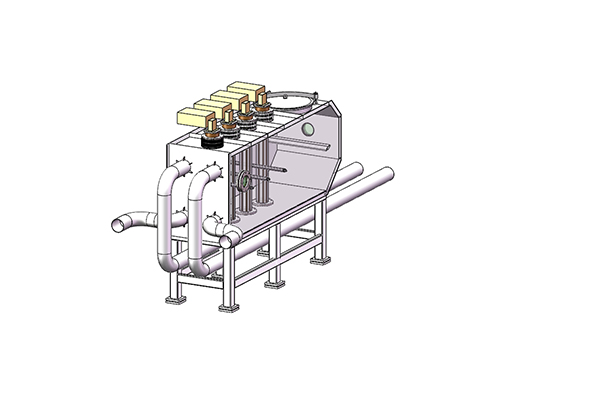
VOCS catalytic combustion waste gas treatment equipment in paint shop: Catalytic combustion equipment is a kind of deodorization and deodorization waste gas treatment equipment. The concept of catalytic combustion is to use the catalytic incineration reaction of combustibles under the effect of catalyst and certain temperature conditions. Combustibles are burned under the effect of catalyst. Compared with direct incineration, catalytic incineration has a lower temperature and is quite safe. Catalytic principle and equipment composition (1) Catalyst is defined as a substance that can improve the rate of chemical reaction, control the direction of reaction, and keep its chemical properties unchanged before and after reaction. (2) The mechanism of catalytic effect The mechanism of catalytic effect is a very complicated problem, which is only briefly introduced here. In a chemical reaction process, the participation of the catalyst cannot change the original chemical balance, but only the speed of the chemical reaction. Before and after the reaction, the nature of the catalyst itself does not change. So, how does the catalyst speed up the response? The catalyst has not changed before and after the reaction, so has the catalyst participated in the reaction? In practice, the catalyst itself has participated in the reaction. It is because of its participation that the reaction has changed the original path, reduced the activation energy, and then accelerated the reaction speed. For example, the reaction A+B → C is transited through the central active complex (AB), that is, the reaction speed of A+B → [AB] → C is slow. After participating in catalyst K, the reaction is completed in an easy way: A+B+2K → [AK]+[BK] → [CK]+K → C+2K center no longer needs the transition from [AB] to C, and then the reaction speed is accelerated without changing the catalyst properties. (3) Process composition of catalytic incineration equipment: different emission occasions and different exhaust gases have different process flows. However, no matter which process flow is adopted, it is composed of the following process units. ① Waste gas pretreatment In order to avoid blocking of the catalyst bed and catalyst poisoning, it is necessary to pretreat the waste gas before entering the bed to remove the dust, droplets and catalyst poisons in the waste gas. ② Preheating equipment Preheating equipment includes waste gas preheating equipment and catalyst incinerator preheating equipment. Because all catalysts have a catalytic activity temperature, it is called catalyst ignition temperature for catalytic incineration. It is necessary to make the temperature of exhaust gas and bed reach the ignition temperature before catalytic incineration. Therefore, it is necessary to set up preheating equipment. However, for occasions where the exhaust gas temperature is high, such as enameled wire, insulating material, baking varnish, etc., and the temperature can reach more than 300 ℃, preheating equipment is not required. The hot gas heated by the preheating equipment can be arranged in the heat exchanger and bed. The heat source of the preheater can be flue gas or electric heating, and now electric heating is more used. When catalytic reaction begins, exhaust gas can be preheated with recovered reaction heat as far as possible. In the case of high reaction heat, waste heat recovery equipment should also be set to save power. The heat source temperature of preheated exhaust gas generally exceeds the catalyst activity temperature. In order to maintain the catalyst, the heating equipment should be kept a certain distance from the catalytic incineration equipment, so that the exhaust gas temperature can be evenly distributed. Starting from the need for preheating, catalytic incineration is applicable to the purification of continuous exhaust. If intermittent exhaust, not only each preheating needs energy, but also the reaction heat can not be recycled, which will result in great power waste. This should be noted in planning and selection. ③ Fixed bed catalytic reverberator is generally selected as catalytic incineration equipment. The planning of the reverberator shall be carried out according to the standard, which shall be convenient for operation, repair and catalyst loading and unloading. In the process planning of catalytic incineration, it is necessary to plan the built-up process of components according to the specific situation in the case of large air volume, that is, the preheater and the reverberator are installed separately, and the pipes are connected between them. For occasions with small air volume, catalytic incinerators can be selected to combine preheating and reaction, but pay attention to the distance between preheating section and reaction section. In the catalytic incineration of organic waste gas, the organic waste gas to be treated is easy to explode when mixed with air at high temperature, so the safety problem is very important. Therefore, on the one hand, it is necessary to control the mixing ratio of organic matter and air to keep it at the lower explosive limit; On the other hand, the catalytic incineration system should be equipped with monitoring and alarm equipment and explosion-proof measures.
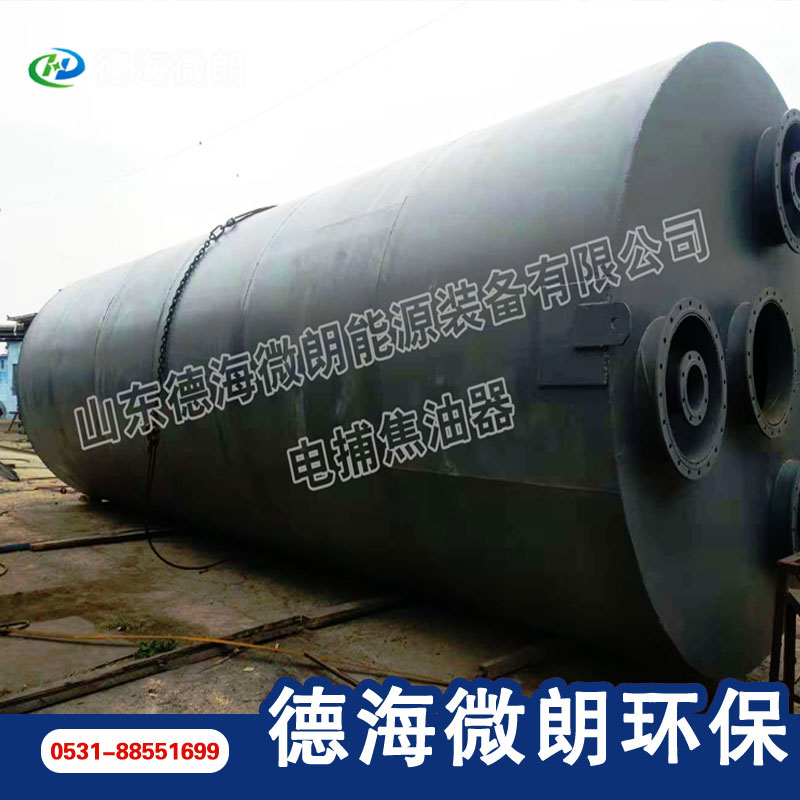
UV disinfection is generally only used for air and instrument surface disinfection. Surgical dressings cannot be treated by UV radiation as a routine method. Ultraviolet radiation is the general term of radiation in electromagnetic spectrum with wavelength from 10nm to 400nm, which can not cause people's vision. In 1801, German physicist Ritter found that the ultraviolet ray could sensitize the photographic negative containing silver bromide at the outer part of the ultraviolet end of the sunlight spectrum, so he found the existence of ultraviolet ray. Too much ultraviolet rays entering the body will cause skin cancer. production Silver ion sterilization It can be disinfected after use every day. It should be disinfected two or three times a week. It is recommended that the toothbrush head should be replaced every three months. It can be disinfected every day. The SEGA toothbrush sterilizer I selected should be disinfected for 6-8 minutes each time. It is a good ultraviolet disinfection lamp. It needs to be equipped with a ballast. Mould formation is due to long-term lack of ventilation and humidity, Silver ion sterilization manufactor If ventilation and moisture removal are available, mold will not grow. Since mold has been formed, first kill it with a mold remover, and then put a moisture bag such as a charcoal bag. I often do on-site mildew and odor removal projects. You can sprinkle lime on the corner of the wall or place charcoal in the house to absorb moisture when the house is wet. In addition, don't open the window in foggy or rainy weather. Open the window in good weather to ventilate in time.
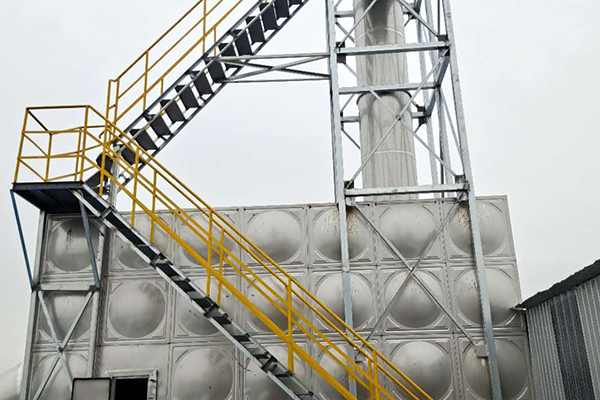
working principle: The thermal storage catalytic combustion equipment uses natural gas to directly burn organic waste gas. Under the temperature of 750~850 ℃, organic molecules are decomposed into CO2 and H2O. The burned flue gas accumulates heat in the ceramic through the thermal storage ceramic brick, preheats the organic waste gas, and then discharges it. The inlet and outlet directions of the waste gas are automatically switched by the switch valve, and work circularly, RTO can fully recover and burn organic decomposition heat energy, which greatly reduces the energy consumption of the system. Catalytic combustion equipment is applicable to industries: Applicable to the treatment of mixed combustible organic waste gas and odor with large and medium concentration (thousands of ppm) and medium air volume Applicable to waste gas treatment in paint shop Applicable to waste gas treatment of electronic product manufacturing and integrated circuit Applicable to waste gas treatment in printing process and injection molding process Applicable to the treatment of organic waste gas generated in petrochemical, medical and other industries Technical features of regenerative catalytic combustion equipment: Wide range of exhaust gas; High waste gas treatment efficiency; Less maintenance work, safe and reliable; Low pressure loss and high purification efficiency; Long service life of equipment; Low operation cost