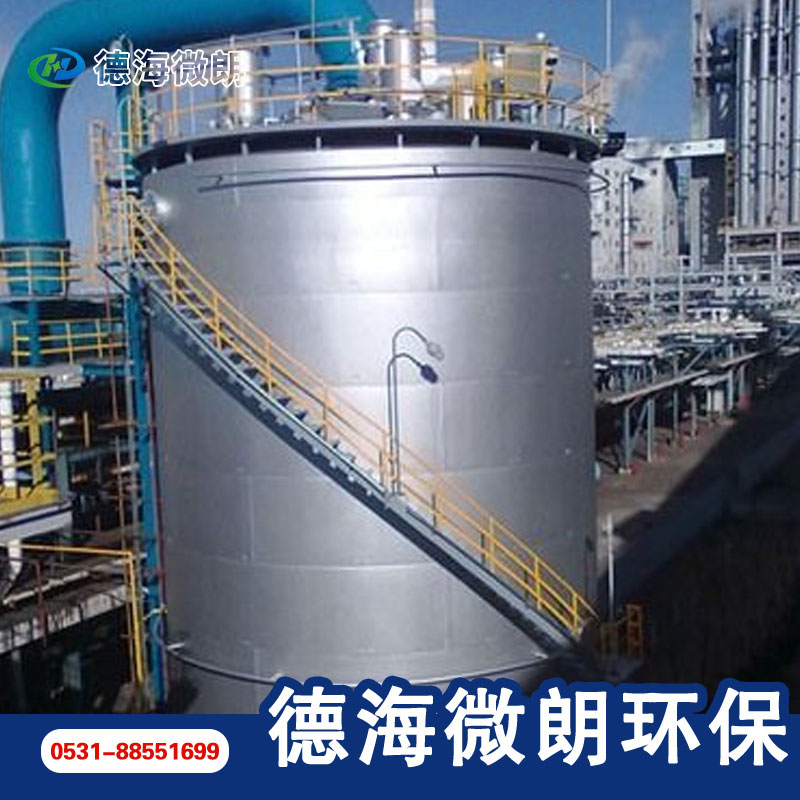
RCO organic waste gas catalytic combustion purification equipment can effectively purify the environment, pollution, improve labor operating conditions, ensure the health of workers, and the heat emitted can be recycled to reduce production costs. RCO organic waste gas catalytic combustion equipment has perfect system design, complete auxiliary equipment, high purification efficiency and high automation. RCO organic waste gas catalytic combustion equipment RCO organic waste gas catalytic combustion purification device is designed based on two basic principles of adsorption and catalytic combustion, namely adsorption concentration catalytic combustion method. The dedusting equipment adopts the working mode of single bed adsorption purification of organic waste gas and catalytic combustion device regeneration and activation of activated carbon. Firstly, the organic waste gas with low concentration is adsorbed by activated carbon, and the adsorption operation is stopped when it is almost saturated, then the organic matter is desorbed from the activated carbon by hot gas flow to regenerate the activated carbon; The desorbed organic matter has been concentrated (the concentration is dozens of times higher than the original) and sent to the catalytic combustion chamber for catalytic conversion into CO2 and H2O for emission; When the concentration of organic waste gas reaches above 2000ppm, the organic waste gas can maintain spontaneous combustion in the catalytic bed without external heating. Part of the burned tail gas is discharged into the atmosphere, and most of it is sent to the adsorption bed for desorption and regeneration of activated carbon. In this way, the heat energy required for combustion and desorption can be met to save energy. The regenerated activated carbon can be used for the next adsorption.? RCO organic waste gas catalytic combustion equipment uses catalytic combustion method to convert toxic and harmful organic gas into non-toxic gas.? The main structure of RCO organic waste gas catalytic combustion equipment is composed of three major parts: purification device host, induced draft fan and control system. The catalytic combustion purification device includes: dedusting flame arrester, heat exchanger, preheater and catalytic combustion chamber. The organic waste gas enters the preprocessor from the air inlet at the upper part of the equipment, passes through the coarse filter element composed of multi-layer stainless steel wire mesh to remove dust and other particles in the waste gas, and enters the combined adsorption bed from the main channel at the lower part of the device (two rows in parallel with six grids). Each adsorption bed is equipped with a set of pneumatic switch valve, which can change the adsorption bed into adsorption/desorption state. The longitudinal section of the adsorption bed from bottom to top is respectively the inlet manifold, adsorption chamber, air purification chamber and outlet manifold. The adsorption chamber and the air purification chamber are separated by a flower plate, under which a number of adsorption cylinders are hoisted. The waste gas entering the adsorption chamber passes through the adsorption layer through the outer wall of the adsorption cylinder, VOCs molecules are adsorbed by a large number of microporous surfaces of the adsorbent. After being purified, the waste gas enters the purification chamber upward through the flower plate hole, and then enters the gas outlet header through the switching valve and is discharged by the fan. One of the six adsorption chambers must be in the desorption state, and the other five must be in the adsorption state. Generally, the desorption time is 12 minutes, that is, the adsorption bed responsible for the adsorption work can be desorbed and regenerated once every hour. This work process of the device coincides with the name of the invention zhuanli - a kind of compartment offline desorption bag type adsorption equipment. Its process principle is the same as that of the pulse reverse blow compartment offline bag type dust collector, except that the purification process of the device is "physical adsorption", The bag filter purification process is "physical filtration". The desorption working medium of the adsorption bed is hot air, which is provided by the catalytic combustion device. Generally, the temperature of the hot air is ≤ 150 ℃, which is determined by the boiling point of different VOCs and the saturated vapor partial pressure at the desorption temperature.
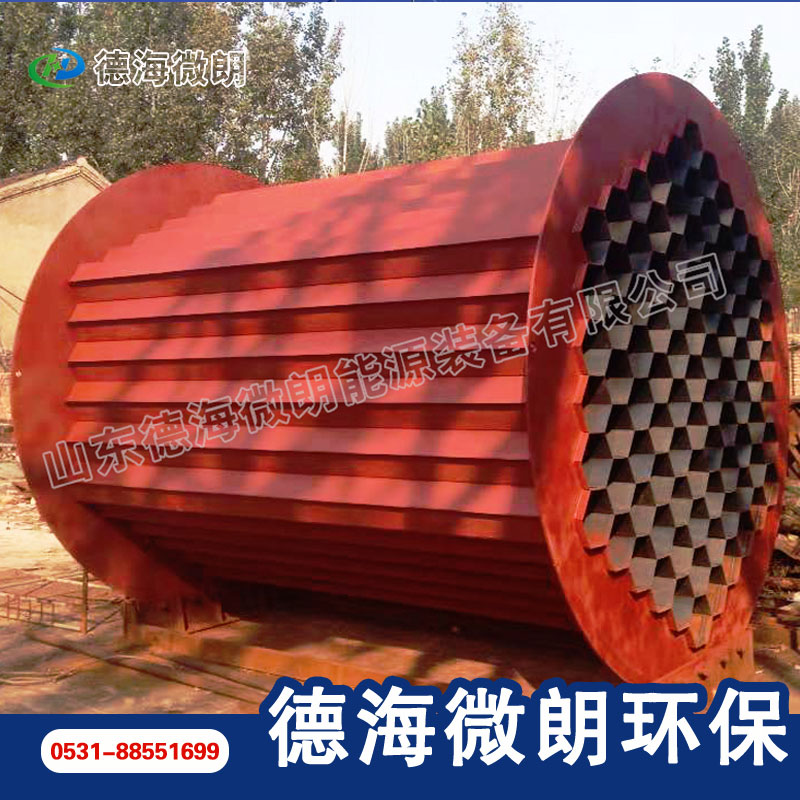
The catalytic combustion equipment for waste gas treatment is mainly used as a supporting part of the catalytic bed electric heating oxidation combustion system in the CO/RCO adsorption+desorption+catalytic combustion system. It is widely applicable to the purification and odor elimination of hazardous waste gas volatilized or leaked from painting, printing, household appliances, footwear, plastics and various chemical workshops, and is suitable for low concentration (1501000) The organic waste gas that is not suitable for direct combustion or catalytic combustion and recovery treatment will be concentrated by activated carbon adsorption, and then the high concentration organic waste gas will be removed through the desorption procedure and sent to the unit for thermal oxidation reaction. The self heating effect of the organic waste gas catalytic reaction can greatly reduce the heat consumption of the electric heater, especially for the treatment sites with large air volume, Satisfactory economic and social benefits can be obtained. Application scope of exhaust gas catalytic combustion equipment: 1. Industrial applications: common pollutants discharged from petrochemical, light industry, plastics, printing, coating and other industries; 2. Waste gas type application: hydrocarbon compounds (aromatics, alkanes, olefins), benzene, ketones, phenols, alcohols, ethers, alkanes and other compounds; Features of catalytic combustion equipment for waste gas treatment: 1. Convenient operation: fully automatic control during operation. 2. Low energy consumption: during normal operation, the equipment operates at low power (or no power) because the exhaust gas has some concentration. 3. Stable performance: pressure relief and self protection, fire resistance and dust removal, over temperature alarm and automatic control. 4. Low resistance: honeycomb ceramic catalyst impregnated with today's advanced precious metal palladium and platinum has a large specific surface area. 5. Small floor area: only 70% of the same products in the same industry. 6. Long service life: the catalyst is usually replaced within 4 years
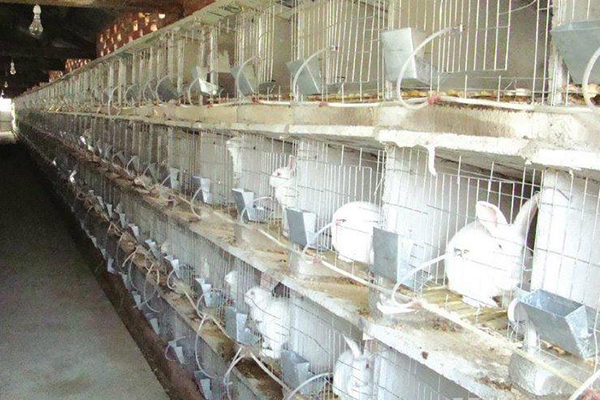
VOCS catalytic combustion waste gas treatment equipment in paint shop: Catalytic combustion equipment is a kind of deodorization and deodorization waste gas treatment equipment. The concept of catalytic combustion is to use the catalytic incineration reaction of combustibles under the effect of catalyst and certain temperature conditions. Combustibles are burned under the effect of catalyst. Compared with direct incineration, catalytic incineration has a lower temperature and is quite safe. Catalytic principle and equipment composition (1) Catalyst is defined as a substance that can improve the rate of chemical reaction, control the direction of reaction, and keep its chemical properties unchanged before and after reaction. (2) The mechanism of catalytic effect The mechanism of catalytic effect is a very complicated problem, which is only briefly introduced here. In a chemical reaction process, the participation of the catalyst cannot change the original chemical balance, but only the speed of the chemical reaction. Before and after the reaction, the nature of the catalyst itself does not change. So, how does the catalyst speed up the response? The catalyst has not changed before and after the reaction, so has the catalyst participated in the reaction? In practice, the catalyst itself has participated in the reaction. It is because of its participation that the reaction has changed the original path, reduced the activation energy, and then accelerated the reaction speed. For example, the reaction A+B → C is transited through the central active complex (AB), that is, the reaction speed of A+B → [AB] → C is slow. After participating in catalyst K, the reaction is completed in an easy way: A+B+2K → [AK]+[BK] → [CK]+K → C+2K center no longer needs the transition from [AB] to C, and then the reaction speed is accelerated without changing the catalyst properties. (3) Process composition of catalytic incineration equipment: different emission occasions and different exhaust gases have different process flows. However, no matter which process flow is adopted, it is composed of the following process units. ① Waste gas pretreatment In order to avoid blocking of the catalyst bed and catalyst poisoning, it is necessary to pretreat the waste gas before entering the bed to remove the dust, droplets and catalyst poisons in the waste gas. ② Preheating equipment Preheating equipment includes waste gas preheating equipment and catalyst incinerator preheating equipment. Because all catalysts have a catalytic activity temperature, it is called catalyst ignition temperature for catalytic incineration. It is necessary to make the temperature of exhaust gas and bed reach the ignition temperature before catalytic incineration. Therefore, it is necessary to set up preheating equipment. However, for occasions where the exhaust gas temperature is high, such as enameled wire, insulating material, baking varnish, etc., and the temperature can reach more than 300 ℃, preheating equipment is not required. The hot gas heated by the preheating equipment can be arranged in the heat exchanger and bed. The heat source of the preheater can be flue gas or electric heating, and now electric heating is more used. When catalytic reaction starts, exhaust gas can be preheated with recovered reaction heat as far as possible. In the case of high reaction heat, waste heat recovery equipment should also be set to save power. The heat source temperature of preheated exhaust gas generally exceeds the catalyst activity temperature. In order to maintain the catalyst, the heating equipment should be kept a certain distance from the catalytic incineration equipment, so that the exhaust gas temperature can be evenly distributed. Starting from the need for preheating, catalytic incineration is applicable to the purification of continuous exhaust. If intermittent exhaust, not only each preheating needs energy, but also the reaction heat can not be recycled, which will result in great power waste. This should be noted in planning and selection. ③ Fixed bed catalytic reverberator is generally selected as catalytic incineration equipment. The planning of the reverberator shall be carried out according to the standard, which shall be convenient for operation, repair and catalyst loading and unloading. In the process planning of catalytic incineration, it is necessary to plan the built-up process of components according to the specific situation in the case of large air volume, that is, the preheater and the reverberator are installed separately, and the pipes are connected between them. For occasions with small air volume, catalytic incinerators can be selected to combine preheating and reaction, but pay attention to the distance between preheating section and reaction section. In the catalytic incineration of organic waste gas, the organic waste gas to be treated is easy to explode when mixed with air at high temperature, so the safety problem is very important. Therefore, on the one hand, it is necessary to control the mixing ratio of organic matter and air to keep it at the lower explosive limit; On the other hand, the catalytic incineration system should be equipped with monitoring and alarm equipment and explosion-proof measures.
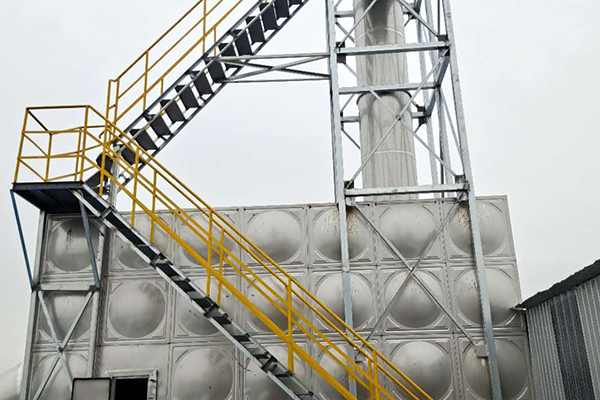
1. Food and beverage - ultraviolet disinfection system helps to meet the water quality standards stipulated by the Food and Drug Administration 2. Biopharmaceuticals - water used for drugs and medical products and on-site cleaning must be free of chlorine, ozone, pathogens and other chemicals. Most pharmaceutical companies rely on UV systems for water disinfection. 3. Cosmetics - water free of microorganisms and toxins can ensure the quality and extend the shelf life of cosmetics. UV sterilization is the choice of the cosmetics industry. 4. Centralized drinking water - UV drinking water disinfection system is a simple and economical solution, which can ensure that every faucet in your home or office is pure 5. Wastewater disinfection and reuse - to solve the problem of water shortage and rising cost of fresh water, Customized Microwave drying of cereals UV disinfection can help by treating wastewater in the third stage. The UV system specially designed for waste water can therefore disinfect waste water so that water can be reused for secondary purposes, such as washing and gardening. 6. Swimming Pools – Chlorine has traditionally been used to ensure clean water in swimming pools. However, more and more people know that through chemical disinfection, chemicals react with many other organic substances to form hundreds of new harmful chemicals. Ultraviolet is a technology without chemical substances, which is considered to be safer Microwave drying of cereals manufactor More cost-effective disinfection methods for swimming pools.
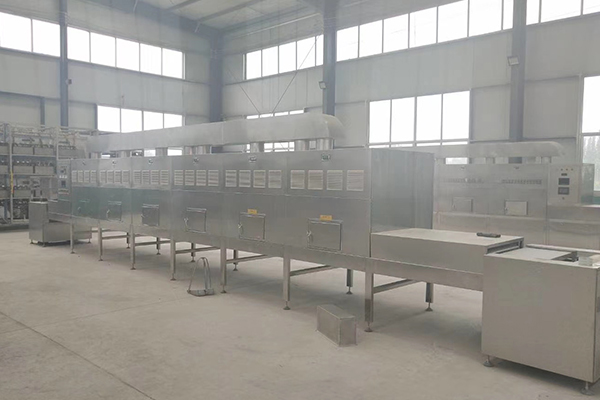
Domestic sewage industrial sewage integration equipment Application industries: municipal sewage, pharmaceutical and chemical sewage, food processing industry sewage, grease, garbage, printing and dyeing prevention industry, wastewater phosphorus removal engineering, environmental protection sewage treatment and other industries. . Precision filtration equipment Application industry: It is used for liquid purification such as water and paint, solid-liquid separation in machinery, metallurgy, chemical industry, prevention and control, printing, electric lock, medicine, food and other industries, food and beverage, fruit wine, biochemical water treatment, high-end aquaculture, etc.