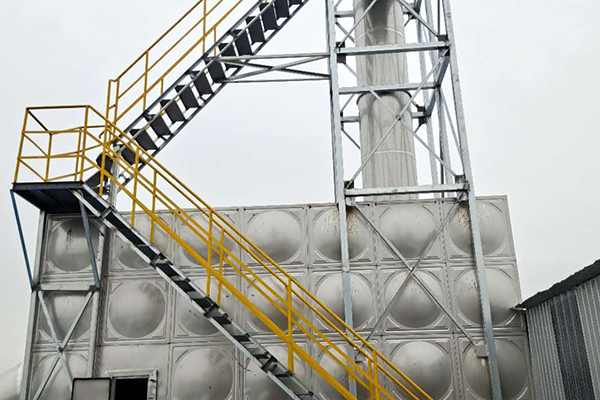
VOCS catalytic combustion waste gas treatment equipment in paint shop: Catalytic combustion equipment is a kind of deodorization and deodorization waste gas treatment equipment. The concept of catalytic combustion is to use the catalytic incineration reaction of combustibles under the effect of catalyst and certain temperature conditions. Combustibles are burned under the effect of catalyst. Compared with direct incineration, catalytic incineration has a lower temperature and is quite safe. Catalytic principle and equipment composition (1) Catalyst is defined as a substance that can improve the rate of chemical reaction, control the direction of reaction, and keep its chemical properties unchanged before and after reaction. (2) The mechanism of catalytic effect The mechanism of catalytic effect is a very complicated problem, which is only briefly introduced here. In a chemical reaction process, the participation of the catalyst cannot change the original chemical balance, but only the speed of the chemical reaction. Before and after the reaction, the nature of the catalyst itself does not change. So, how does the catalyst speed up the response? The catalyst has not changed before and after the reaction, so has the catalyst participated in the reaction? In practice, the catalyst itself has participated in the reaction. It is because of its participation that the reaction has changed the original path, reduced the activation energy, and then accelerated the reaction speed. For example, the reaction A+B → C is transited through the central active complex (AB), that is, the reaction speed of A+B → [AB] → C is slow. After participating in catalyst K, the reaction is completed in an easy way: A+B+2K → [AK]+[BK] → [CK]+K → C+2K center no longer needs the transition from [AB] to C, and then the reaction speed is accelerated without changing the catalyst properties. (3) Process composition of catalytic incineration equipment: different emission occasions and different exhaust gases have different process flows. However, no matter which process flow is adopted, it is composed of the following process units. ① Waste gas pretreatment In order to avoid blocking of the catalyst bed and catalyst poisoning, it is necessary to pretreat the waste gas before entering the bed to remove the dust, droplets and catalyst poisons in the waste gas. ② Preheating equipment Preheating equipment includes waste gas preheating equipment and catalyst incinerator preheating equipment. Because all catalysts have a catalytic activity temperature, it is called catalyst ignition temperature for catalytic incineration. It is necessary to make the temperature of exhaust gas and bed reach the ignition temperature before catalytic incineration. Therefore, it is necessary to set up preheating equipment. However, for occasions where the exhaust gas temperature is high, such as enameled wire, insulating material, baking varnish, etc., and the temperature can reach more than 300 ℃, preheating equipment is not required. The hot gas heated by the preheating equipment can be arranged in the heat exchanger and bed. The heat source of the preheater can be flue gas or electric heating, and now electric heating is more used. When catalytic reaction starts, exhaust gas can be preheated with recovered reaction heat as far as possible. In the case of high reaction heat, waste heat recovery equipment should also be set to save power. The heat source temperature of preheated exhaust gas generally exceeds the catalyst activity temperature. In order to maintain the catalyst, the heating equipment should be kept a certain distance from the catalytic incineration equipment, so that the exhaust gas temperature can be evenly distributed. Starting from the need for preheating, catalytic incineration is applicable to the purification of continuous exhaust. If intermittent exhaust, not only each preheating needs energy, but also the reaction heat can not be recycled, which will result in great power waste. This should be noted in planning and selection. ③ Fixed bed catalytic reverberator is generally selected as catalytic incineration equipment. The planning of the reverberator shall be carried out according to the standard, which shall be convenient for operation, repair and catalyst loading and unloading. In the process planning of catalytic incineration, it is necessary to plan the built-up process of components according to the specific situation in the case of large air volume, that is, the preheater and the reverberator are installed separately, and the pipes are connected between them. For occasions with small air volume, catalytic incinerators can be selected to combine preheating and reaction, but pay attention to the distance between preheating section and reaction section. In the catalytic incineration of organic waste gas, the organic waste gas to be treated is easy to explode when mixed with air at high temperature, so the safety problem is very important. Therefore, on the one hand, it is necessary to control the mixing ratio of organic matter and air to keep it at the lower explosive limit; On the other hand, the catalytic incineration system should be equipped with monitoring and alarm equipment and explosion-proof measures.
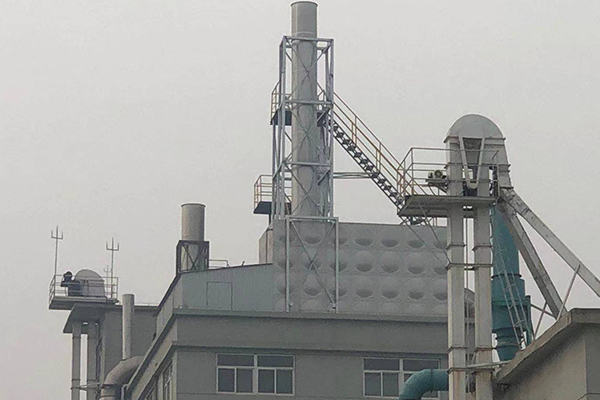
1. Food and beverage - ultraviolet disinfection system helps to meet the water quality standards stipulated by the Food and Drug Administration 2. Biopharmaceuticals - water used for drugs and medical products and on-site cleaning must be free of chlorine, ozone, pathogens and other chemicals. Most pharmaceutical companies rely on UV systems for water disinfection. 3. Cosmetics - water free of microorganisms and toxins can ensure the quality and extend the shelf life of cosmetics. UV sterilization is the choice of the cosmetics industry. 4. Centralized drinking water - UV drinking water disinfection system is a simple and economical solution, which can ensure that every faucet in your home or office is pure 5. Wastewater disinfection and reuse - to solve the problem of water shortage and rising cost of fresh water, new type Microwave drying of cereals UV disinfection can help by treating wastewater in the third stage. The UV system specially designed for waste water can therefore disinfect waste water so that water can be reused for secondary purposes, such as washing and gardening. 6. Swimming Pools – Chlorine has traditionally been used to ensure clean water in swimming pools. However, more and more people know that through chemical disinfection, chemicals react with many other organic substances to form hundreds of new harmful chemicals. Ultraviolet is a technology without chemical substances, which is considered to be safer Microwave drying of cereals programme More cost-effective disinfection methods for swimming pools.
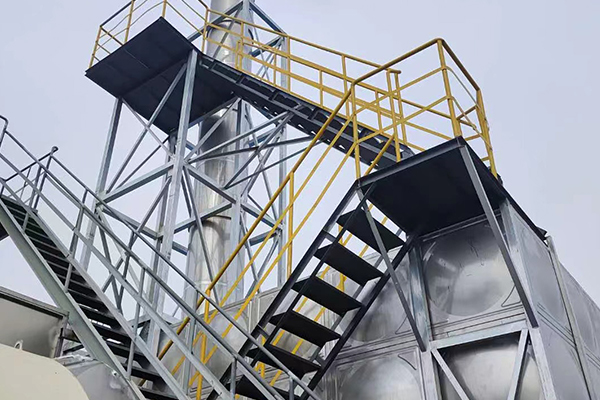
After years of development, microwave electrodeless UV sterilization equipment has been widely used in drinking water, food, beverages, electronic products, chemicals, medicine, sewage microwave UV water treatment equipment and other fields. Microwave drying of cereals programme High intensity odorless UV germicidal lamp is used to simplify the special stainless steel inner wall, so that the pretreated water has enough UV when passing through the UV. new type Microwave drying of cereals Irradiation has good sterilization effect. In addition, it has the advantages of simplicity, convenience, broad-spectrum, no secondary pollution, convenient management and automation.
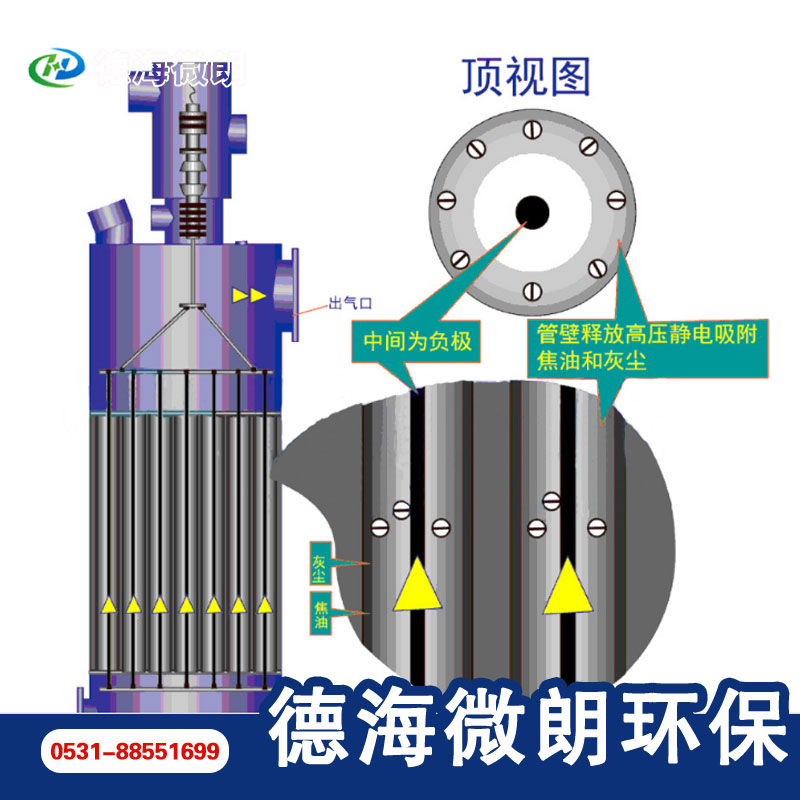
The sterilization principle of microwave electrodeless ultraviolet sterilization equipment is to use the sterilization ability of ultraviolet light. Can ultraviolet light directly kill microorganisms? Microwave drying of cereals programme According to different biological effects, ultraviolet light is generally divided into four parts according to wavelength: A-band (UV-A), new type Microwave drying of cereals Also known as black spot effect ultraviolet (400 ~ 320 nm); B band (UV-B), also known as erythema effect ultraviolet (320 ~ 275 nm); C-band (UV-C), also known as sterilization ultraviolet (275 ~ 200 nm); D-band (UV-D), also known as vacuum ultraviolet ray (200-100 nm). C-band ultraviolet light is mainly used for water disinfection.
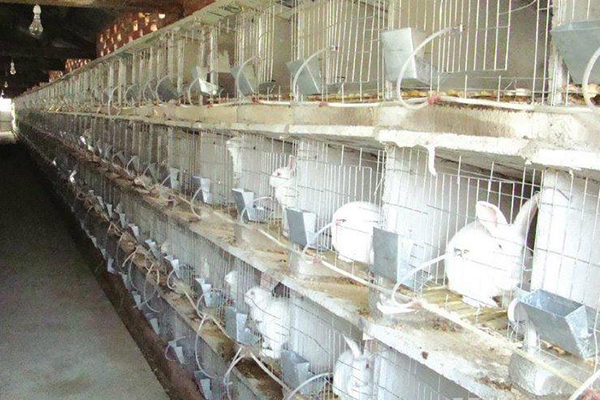
Microwave and ultraviolet water treatment equipment can improve heat exchange efficiency, save energy and reduce consumption. new type Microwave drying of cereals The deposits on the surface of the cooler rise by 0. mm every time, High efficiency of heat exchanger can generally reduce 20-30%, and power consumption will increase 4-8%. The selection of organic chemical dosing method can maintain the equipment and extend the service life of the equipment. The etching rate of carbon steel by cooling circulating water without microwave ultraviolet water treatment equipment exceeds 0.5mm/a, Microwave drying of cereals programme The corrosion rate of the solved cooling circulating water on carbon steel is less than 0. mm/a, which can reasonably maintain the equipment and extend the service life of the equipment. Reduce the frequency of routine maintenance to ensure normal operation.
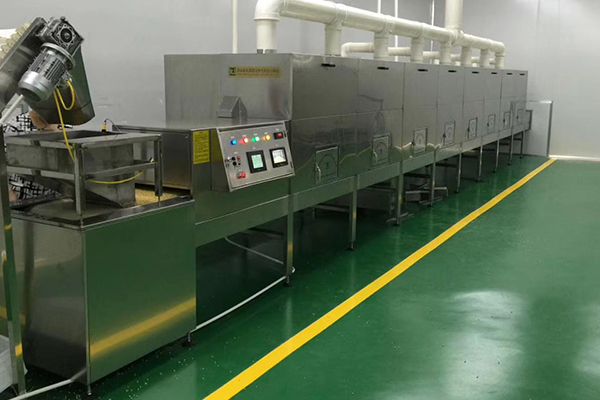
In the daily treatment of sewage, many people think that sewage management needs high costs, so they improve on the basis of sewage ultraviolet disinfection equipment in large cities. But suburban residents or residents far away from the city center are often excluded because the pipeline design is not perfect, new type Microwave drying of cereals They will be discharged indiscriminately, resulting in more serious urban pollution. Microwave drying of cereals programme At present, the public's attention to microwave and ultraviolet water treatment equipment for pollution, coupled with the adjustment of China's and cities' systems, supervises urban emissions and investment in microwave and ultraviolet water treatment equipment for urban pollution. The emergence of ultraviolet disinfection equipment for domestic sewage not only makes the public find that the investment cost is low, but also the treatment efficiency is relatively high.